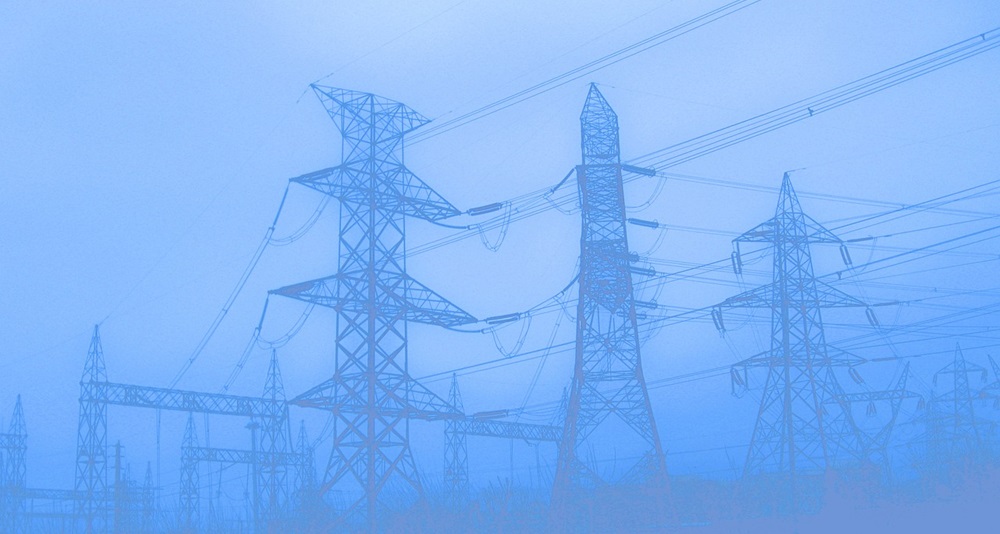
Several years ago, connecting equipment to the internet and extrapolating usable information and data from those machines was a costly and time-consuming process that only large businesses could easily justify. Today, prices on IoT hardware and software platforms are coming down, allowing business in all types of industries to be a part of the “industrial IoT revolution,” so to speak. The average cost of an industrial IoT sensor in 2004 was $1.30. By 2016 it was about 50 cents and should fall below 40 cents by 2020.
Much like consumers can buy a smart thermostat to automate their air conditioning and quickly see their energy bills fall, businesses can invest in pre-built IoT hardware and software platforms that aren’t exorbitantly expensive and will quickly generate a return on their IoT investment. IoT terminals remove several engineering, hardware design and certification challenges that once made it difficult for small and mid-sized businesses to connect equipment – whether a few pieces or a few thousand – in a cost-effective and timely manner via cellular connections. While bespoke solutions might take 12 to 18 months to design and deploy, IoT terminals can help businesses connect their equipment within 3 to 6 months.
Software integration is now the only real hurdle companies need to jump when they purchase IoT terminals. Terminals operate via AT commands that communicate with a cellular network, establish a connection and transmit data between sensors and a software platform from which businesses can extract actionable insights about their equipment’s performance, health, utilization and efficiency.
What data businesses collect and how they use it is really limited by their imagination. Manufacturers may want to collect data about resource availability; if they’re holding raw materials for long periods of time it’s likely they are over-ordering and can reduce order volume or frequency to save money and reclaim usable warehouse space. Similarly, monitoring the volume of products ready for pickup and delivery can help manufacturers schedule pickups and deliveries more accurately and save money on logistics.
One of the most effective ways manufacturers can use the IoT is to connect machines on the factory floor to monitor their performance and maintenance needs to avoid workflow interruptions. Preventative maintenance is much more cost effective than performing on site repairs once a machine is down, and a better view of their needs can help companies schedule equipment maintenance in a way that minimizes disruption.
Utilities providers can similarly monitor the health of their distribution networks to minimize waste and proactively react to maintenance needs. They’ll also save money on fuel by dispatching maintenance teams only when needed, rather than at regular intervals for “spot checks.” Usage of water and electricity can also be monitored remotely, helping businesses bill more effectively and save more money on fuel and labor costs.
Again, these benefits can be had by identifying the right data needed to analyze a problem and make a change. Some businesses might have developers in-house who can do that, but it is usually most cost-effective to have third-party consultants help plan out data targets, install and configure sensors and develop data visualization platforms to turn raw data from equipment into digestible business insights.
IoT consultants can not only help to bring devices online to communicate with software platforms and start turning raw data into actionable insights, they’ll also help businesses chart a course toward automated adjustments to their supply chain, processing and deliveries. Then, just like a smart home thermostat can sense your preferences and automatically cool your home at night or kick into energy-save mode while you’re at work, industrial IoT devices can be automated to make more efficient use of raw materials, increase total utilization rates or perhaps even one day to repair themselves when problems occur.
About the author: Scott Parish has worked in the semiconductor and IoT industry for 30 years and today manages Gemalto’s North American IoT channel. When he’s not working, he enjoys mountain biking, boating and deep-sea fishing. He can be reached at [email protected] for more information on Gemalto’s terminal products or to just say hello.
Edited by
Ken Briodagh