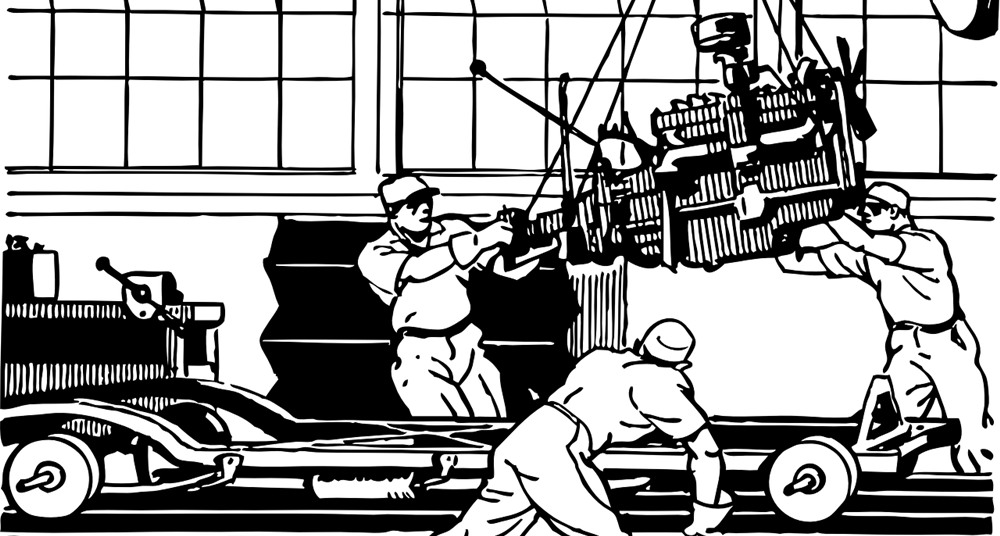
Like any other iteration of “smart” technology, smart manufacturing is meant to transform the industry into something more automated, efficient and cost-effective. Through the use of IoT devices, connected machinery, and data-driven operations, manufacturers have the opportunity to develop remarkable things. As a result, unprecedented levels of productivity and output are being achieved through such platforms.
But the ultimate benefit is that smarter, more autonomous technologies will supplement the human workforce. These are the people who spend most of their time in or around factories and plants. "cobots," or collaborative robots, for example, will work directly alongside their human counterparts to handle the more tedious or dangerous duties. Human workers are then free to handle more relevant tasks.
Promising or not, the technology is not perfect. The trick is to ensure new deployments actually aid the workforce and the overall operation, as opposed to creating more problems.
Leveraging the Right Data
Think of it like this. You ask a smart robot to make you pizza. It goes to work and creates a questionable-looking anchovy pie with white sauce and gorgonzola cheese. Maybe that sounds delicious to you, but not to us! Technically, the robot didn’t do anything wrong — it made the pizza you asked for. The problem was that it made the wrong type of pizza.
With pizza, the wrong outcome isn’t too bad. You can restart the bot and try again, only with more specific details next time. In manufacturing and development, however, the smallest mistake can have monumental consequences. Apply the scenario to the auto industry and, well, let’s just say you’re going to end up with a vehicle you wouldn’t want to use on open roads.
The pizza scenario above can be solved with one basic element: data. With the right types of data, you can ensure that the robots and systems in place work as intended. This ensures that you don’t end up with a problem such as improper components or materials inside a vehicle.
The more data you have to work with — provided it’s being leveraged in the right ways — the higher your overall efficiency and product quality. Caterpillar partnered up with Uptake to deploy an industrial analytics system for their machinery. During their collaboration, they developed a data-driven system that can be used by customers to better monitor and optimize their machinery and fleets. At the heart of it all is — you guessed it — data.
Okay, so data is important. Or, more specifically, the right data. How does that impact conventional auto manufacturing processes? What is it that “smart” systems will offer?
What Does Smart Manufacturing Look Like in the Auto Industry?
Smart manufacturing is the connection or harmonization of varying stages and technologies to improve operations efficiency. It doesn’t necessarily relate to a specific technology or type of device, although there are several common forms of devices used in the field. IoT sensors are a great example.
In auto manufacturing, plants generally contain disparate systems that work together to create a single type of product or vehicle. For instance, you might have IT or computer software, intelligent motors and robotic assemblies, vehicle sensors, additional hardware or even product management systems.
For the most part, however, conventional manufacturing methods see these systems as separate. They are segmented or siloed off from one another. Smart manufacturing will use modern data-sharing technologies to unite these sections of the plant, improving efficiency, reducing costs and boosting output.
As Deloitte elegantly puts it, “[By] shifting from linear, sequential supply chain operations to an interconnected, open system of supply operations — known as the 'digital supply network' — [it will] lay the foundation for how companies compete in the future.”
Furthermore, the technology can be used to track and make precise adjustments during the assembly stage, which allows for a more personalized customer experience. Imagine customers ordering a vehicle through an online storefront and picking the different upgrades or options they want, individually, as opposed to the standard bulk package selection.
How Do You Make This Happen?
Before you can implement any new strategy or system, you must assess the landscape. What kinds of technologies can you leverage to improve efficiency? How can you help your plant workers and make their jobs easier? What innovative forms of customer support are you looking to add? These are all questions that are important when choosing how and what to upgrade within your plant.
In manufacturing, smart sensors are going to offer the most significant benefits. Really, they are no different than conventional sensors — they’re still designed to collect and report data about machinery and equipment, processes or efficiency. What makes them more accessible is the open connection to a local network or data system.
Plus, the information can be reviewed remotely, and altogether automated when combined with machine learning platforms. Traditionally, rotary screw air compressors — used often in automotive applications — are manually operated, for instance. But with smart, connected systems, they can be automated with little to no oversight necessary while retaining reliability and accuracy. Since rotary screw compressors support the movement of robotic arms during the assembly stage of auto production, connecting these robots can help you better predict maintenance downtime and improve manufacturing efficiency.
For a real-world automation example, Audi has developed a self-learning system for stamping operations on press lines. As things are moving, the system will automatically adjust material injections to ensure the right amounts are fed into a press. This results in more reliable and durable components as well as a more sustainable production process with less waste.
The next step is to ensure that there is a persistent connection available to the local network or infrastructure. Each IoT or connected device you deploy is going to need access to your network to report, collect and process data. This also calls for a stable network or internet gateway if you don’t already have one in place.
Jumping off that, you’ll need to ensure you also have the proper data security and network protection in place. This may warrant an in-house IT and security team to monitor and maintain your network. You can always outsource the duties, as well. Along with that comes use of the proper tools like authentication for users accessing the network or systems, firewalls and monitoring tools to take control when there’s a problem, and backup systems to keep data safe in the event of a failure or outage.
Ultimately, it will be up to you and your team of engineers and workers to decide how modern smart systems are deployed within your plants. Just remember: you don’t have to outfit your entire operation in one go. You can take your time, learn the systems and devices, and optimize how your newly connected operations work.
Edited by
Ken Briodagh